Резка поликарбоната лазером
Содержание
Поликарбонат – универсальный стройматериал, используемый для самых разных нужд. Прочный, прозрачный или цветной материал применяют для строительства теплиц и для отделки кухонного фартука. При любых работах пользователь сталкивается с необходимостью резать пластик. Лазерная резка поликарбоната – лучший способ, хотя и относительно дорогостоящий.
Плюсы и минусы лазерной резки поликарбоната
Различают поликарбонат монолитный и сотовый. Сотовый можно нарезать даже обычным канцелярским ножом. Монолитный тип довольно прочен, для его разрезания нужно приложить усилия. Если же из пластика вырезают сложную по конфигурации деталь, с резкой могут возникнуть сложности.
В последнем случае обычные инструменты, например, пила или ножовка по металлу, мало подходят. А вот лазерная резка является идеальным решением. Высокотемпературный плазменный луч диаметром в 0,004 не режет, а расплавляет материал с невероятной точностью и легкостью. Используют для процедуры газовые лазеры мощностью в 50–15000 Вт, что позволяет успешно обрабатывать изделия любой толщины.
Лазерная резка монолитного поликарбоната обладает массой преимуществ:
- луч не режет, а расплавляет материал, соответственно, при резке отходы просто не образуются;
- с помощью лазера выполняют резку пластика любой плотности и толщины;
- раскрой отличается максимально высокой производительностью – до 400 мм/с;
- лазер буквально «запаивает» края при обработке, так что готовое изделие имеет самый совершенный вид – края фрагментов гладкие, ровные, идеально стыкуются;
- лазер позволяет выполнить раскрой материала по самым сложным контурам;
- станки оборудуются микропроцессорами и блоками автоматического управления, это обусловливает абсолютную идентичность полученных деталей вне зависимости от количества копий;
- стоимость услуги вполне доступная и определяется количеством материала, а не сложностью обработки.
К недостаткам метода относится сложная доступность. Лазерную резку предлагают в относительно крупных городах.
Применение технологии лазерной резки
Высокая эффективность, производительность и необычайно высокая точность резки выступают самыми значимыми достоинствами процесса. Они же вместе с другими особенностями обусловливают широкую сферу применения.
В зависимости от мощности луч в состоянии проплавить стройматериал разной прочности, структуры и толщины. Лазерная резка позволяет работать с металлами – как мягкими, так и очень твердыми, с пластиками практически всех видов, даже с деревом. На сегодня лазерный станок – оптимальный и наиболее непопулярный способ раскроя листов материала любого вида. Соответственно, используется метод в самых разных областях:
- изготовление декоративной продукции из пластика и дерева;
- производство рекламных материалов и оборудования. Чаще всего для таких изделий используется поликарбонат, акриловое стекло, силикатное стекло;
- с помощью лазера можно выполнить не только резку, но и такую тонкую работу, как гравировка, причем степень сложности рисунка значения не имеет, а выполнить такое украшение можно на поверхности любого материала: сталь, медь, дерево, поликарбонат;
- возможность изготавливать предметы самой сложной конфигурации обусловлена применением лазера для получения плоских и объемных фигур, букв, элементов любой формы;
- не менее сложные детали получают на станках из металла, соответственно, такая резка востребована в машинной промышленности при изготовлении элементов высочайшей точности;
- резка поликарбоната и силикатного стекла требуется при производстве торгового и бытового оборудования и мебели.
Ограничением для применения этого способа выступает только большая толщина. Причем к монолитному пластику это отношения не имеет.
Как происходит резка поликарбоната лазером
Технология довольно проста. Большинство этапов резки поликарбоната выполняются автоматически. Процесс включает 3 этапа.
- Вначале создают эскиз. Лучше всего это сделать с помощью подходящей программы – AutoCAD, или Compas, например. По созданному макету и будет производиться резка поликарбоната. Сложность и конфигурация эскиза значения не имеет.
- Подбирается материал – поликарбонат выпускают разной толщины, цвета, степени прозрачности. Только толщина имеет значение для процесса резки, так как для работы с материалом разной плотности требуются лазеры разной мощности. 2 других параметра важны для качественного исполнения заказа: ведь готовое изделие должно удовлетворять определенным эстетическим и функциональным требованиям.
- Сам раскрой поликарбоната выполняется автоматически. Заданный макет со всеми параметрами загружают в управляющий блок станка, размещают и закрепляют на рабочем столе пластик и запускают выполнение. Резка, охлаждение, отвод отработанного газа производится автоматически. Скорость выполнения определяется толщиной и физическими характеристиками поликарбоната.
Настройка лазерного станка выполняется оператором. Параметры осуществления задачи зависят от типа материала. Например, при резке металлизированного поликарбоната следует уменьшить скорость прохождения лазерного луча с тем, чтобы не повредить металлизированный слой.
Заключение
Лазерная резка поликарбоната – оптимальный способ обработки материала. Он обеспечивает максимальную точность раскроя пластика, позволяет получить изделия самой сложной конфигурации и на основе материала любой толщины.

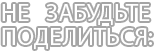